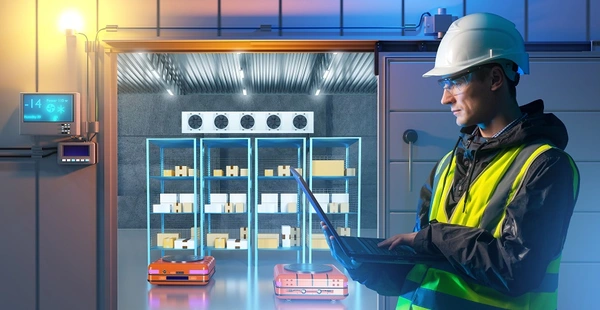
As a product manufacturer, have you ever wondered why some of your product labels stick better than others? The answer lies in the science of label adhesive. Understanding the different types of adhesives and their properties can help you choose the right label adhesive for your product. In this article, I will delve into the science of label adhesive and explain how temperature affects your product labeling.
Introduction to Label Adhesives
Label adhesive is a substance that bonds a label to a surface. It can be classified into two types: permanent and removable. Permanent adhesive is designed to stick to a surface for an extended period, while removable adhesive can be easily peeled off without leaving any residue.
Adhesive is made up of several components, including a polymer, solvent, and additives. The polymer is responsible for the adhesive's tackiness, while the solvent helps make the adhesive more viscous. Additives are added to improve the adhesive's performance, such as UV stabilizers to prevent the adhesive from degrading in sunlight.
Understanding Adhesive Types
Adhesive types can be categorised into four groups: water-based, solvent-based, hot-melt, and radiation-cured. Water-based adhesives are environmentally friendly and have low toxicity. Solvent-based adhesives are highly viscous and have excellent adhesion properties. Hot-melt adhesives are solid at room temperature and become liquid when heated. Radiation-cured adhesives are cured by exposure to radiation, such as ultraviolet light, and are used for high-performance applications.
Each adhesive type has its advantages and disadvantages. For example, water-based adhesives are not suitable for use in humid environments, while hot-melt adhesives can become brittle in cold temperatures. It is essential to choose the right adhesive type for your product based on its intended use and environment.
Adhesion Testing and Measurement
Adhesion testing is the process of measuring how well a label adhesive sticks to a surface. There are several methods for adhesion testing, including peel adhesion, shear adhesion, and tack adhesion. Peel adhesion measures the force required to peel a label off a surface. Shear adhesion measures the force required to slide a label along a surface. Tack adhesion measures the force required to remove a label from a surface immediately after it has been applied.
Adhesion measurement is essential to ensure that your pre-printed label adhesive is performing correctly and to identify any issues before they become a problem. It is also essential to perform adhesion testing on different surfaces to ensure that your label adhesive works on all surfaces.
Factors Affecting Label Adhesive
Several factors can affect label adhesive, including surface energy, surface roughness, and surface contamination. Surface energy is the measure of a surface's ability to attract molecules. A high surface energy surface, such as glass, has a strong attraction to molecules, making it easier for the adhesive to bond. A low surface energy surface, such as plastic, has a weak attraction to molecules, making it more difficult for the adhesive to bond.
Surface roughness can also affect label adhesive. A rough surface has more surface area, making it easier for the adhesive to bond. A smooth surface has less surface area, making it more difficult for the adhesive to bond. Surface contamination, such as dust or oil, can also affect label adhesive by creating a barrier between the adhesive and the surface, preventing the adhesive from bonding correctly.
Temperature's Impact on Label Adhesive
Temperature can significantly affect label adhesive. As temperature increases, the viscosity of the adhesive decreases, making it more fluid and easier to apply. However, as temperature decreases, the viscosity of the adhesive increases, making it more difficult to apply. Cold temperatures can also cause the adhesive to become brittle, resulting in the label peeling or cracking.
High temperatures can also affect label adhesive by causing it to melt or become too fluid, resulting in the label sliding or smudging. It is essential to choose the right adhesive type for your product based on the temperature conditions it will be exposed to.
Understanding the Role of Adhesion Material
Adhesion material is a critical component of label adhesive. It is responsible for the adhesive's bonding properties. Adhesion material can be classified into two types: physical adhesion and chemical adhesion.
Physical adhesion occurs when the adhesive flows into the surface's roughness and creates a mechanical bond. Chemical adhesion occurs when the adhesive bonds to the surface through a chemical reaction. It is essential to choose the right adhesion material for your product based on the surface it will be applied to and the environment it will be exposed to.
Tips on How to Make Stickers Stick Better
If you are experiencing label adhesive problems, there are several tips you can follow to improve the adhesive's performance. First, ensure that the surface is clean and free of any contaminants that can prevent the adhesive from bonding correctly. Second, choose the right adhesive type for your product label based on its environment and use. Third, apply the adhesive at the right temperature to ensure that it flows and bonds correctly. Fourth, perform adhesion testing to identify any issues before they become a problem.
Choosing the Right Label Glue for Your Product
Choosing the right label glue for your product is essential to ensure that your labels stick correctly and do not peel or crack. It is essential to consider the surface the label will be applied to, the environment it will be exposed to, and the application method. For example, if you are applying a label to a low surface energy surface, such as plastic, you may want to choose a solvent-based adhesive that has excellent adhesion properties.
Common Label Adhesive Problems and Solutions
Label adhesive problems can occur for several reasons, including surface contamination, incorrect adhesive type, and incorrect application temperature. If you are experiencing label adhesive problems, some common solutions include cleaning the surface to remove any contaminants, choosing the right adhesive type for your product, and applying the adhesive at the correct temperature.
Conclusion
In conclusion, label adhesive is a critical component of product labeling. Understanding the different adhesive types, adhesion testing, and measurement, and the factors that affect label adhesive can help you choose the right adhesive type for your product. Temperature is a significant factor that can affect label adhesive, and it is essential to choose the right adhesive type for your product based on its temperature conditions. By following the tips and solutions outlined in this article, you can improve your label adhesive's performance and ensure that your customised product labels stick correctly. Ask for more information to learn more about label adhesive and how it can benefit your product.