A Step-By-Step Guide to the Label Making Process
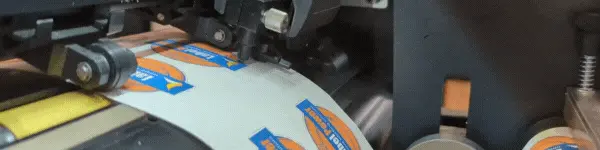
Labels are everywhere, from the packaging on your favorite snacks to the identification tags on your luggage. Have you ever wondered how these labels are made? In this blog, we'll take you on a journey through the label making process, from initial design to the final adhesive application.
1. Design and Artwork Creation
The label making process begins with design and artwork creation. Skilled graphic designers use software to craft visually appealing and informative labels. This stage involves choosing colors, fonts, images, and ensuring that the label effectively communicates its purpose, whether it's for branding, product information, or warnings.
2. Material Selection
Selecting the right label material is crucial. Labels can be made from various materials, including paper, vinyl, polyester, polypropylene and more. The choice depends on factors such as the label's intended use (indoor or outdoor), durability requirements, and the printing method to be used.
Each material comes with their own pros and cons. See here for a breakdown of each one.
3. Printing
Once the design and material are finalized, the label design is printed onto the chosen material. There are several label printing methods used in label making, including:
- Digital Printing: Ideal for short runs and highly detailed designs.
- Flexographic Printing: Suitable for large production runs, especially in the packaging industry.
- Offset Printing: Known for its high-quality results, often used in premium product labeling.
4. Die-Cutting
After printing, the label material is fed through a die-cutting machine. Dies are custom-shaped blades that cut the labels into the desired shape and size. This step is critical for achieving uniform labels.
5. Lamination and Coating
To enhance the label's durability and appearance, lamination or coating may be applied. This can include gloss or matte finishes, UV coatings for added protection, or even embossing for a textured effect.
6. Adhesive Application
Labels need adhesive to stick to surfaces. There are various adhesive types, such as permanent, removable, and repositionable. The choice depends on how long the label needs to adhere and whether it should be easily removable or not.
7. Quality Control and Inspection
Before labels are shipped out, they undergo rigorous quality control and inspection. This ensures that labels meet the specified design, size, and adhesive requirements. Any defects or inconsistencies are identified and corrected.
8. Finishing Touches
Finally, labels may undergo additional processes, such as perforation for easy tear-off labels or sheeting for convenience in certain applications.
The label making process is a meticulous and multifaceted journey that combines artistry and technology. From the initial design concept to the final adhesive application, each step is crucial in producing labels that serve their intended purpose effectively and reliably. The next time you peel off a label, take a moment to appreciate the intricate process behind it, connecting products and information with consumers worldwide.